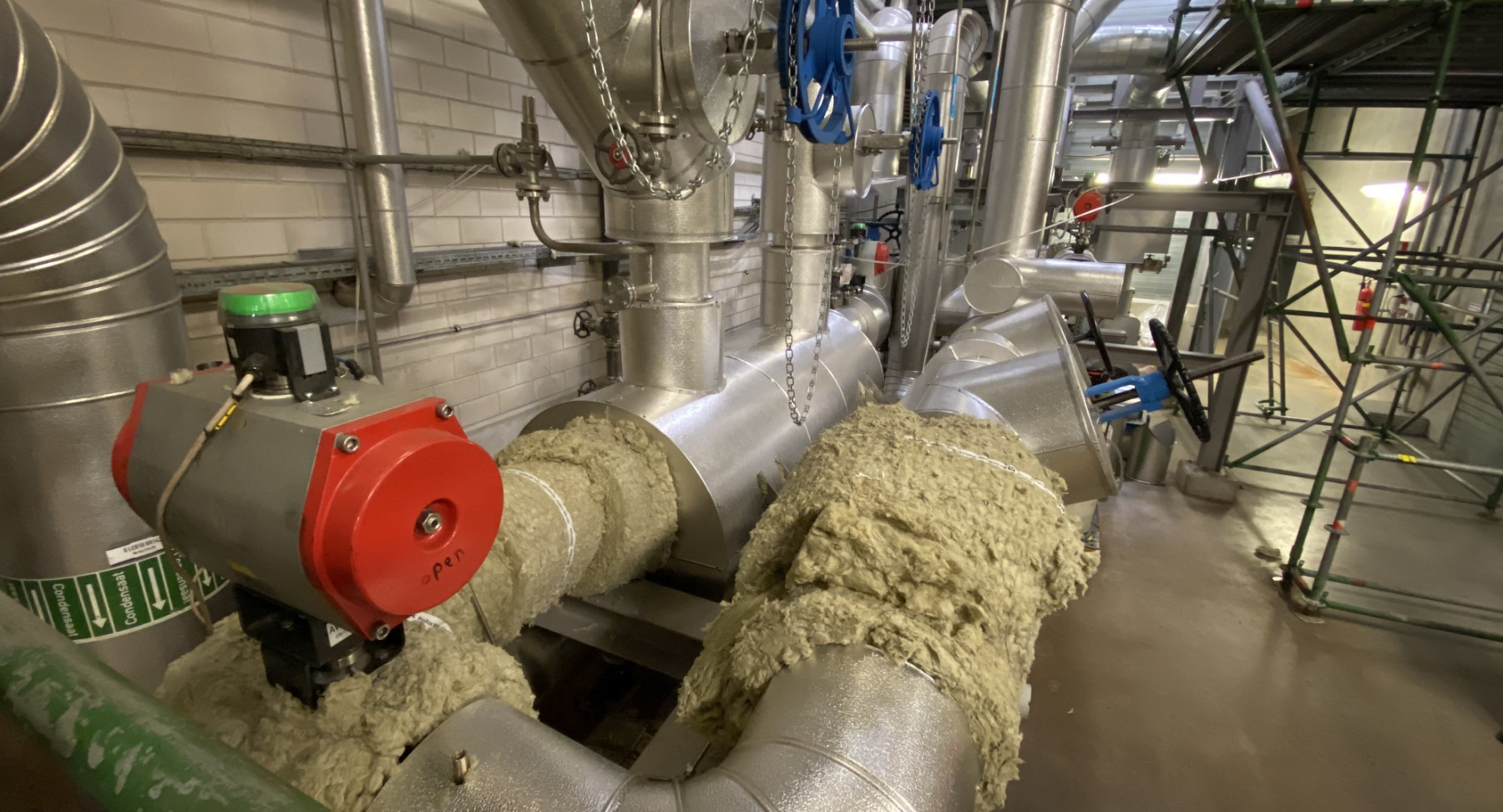
Heat exchanger for waste processing plant
Imagine, you are a project manager at a waste processing company and have to deal with an acute leak in a heat exchanger that is critical for the organization. You immediately contact Kapp for support. Within a day, we get back to you with the first calculations for a replacement heat exchanger. The next day, a Kapp specialist arrives on site to assess the situation. Kapp then delivers the heat exchanger two weeks before the desired delivery date. This is the story of a large waste processing company in North Brabant (NL).
Large temperature changes are a challenge
The company had a 7-year old welded square plate heat exchanger. When problems arose, they had to act quickly; the heat exchanger is critical for cooling flue gases and also ensures that the heat from this flue gas can be reused elsewhere in the process. This heat recovery step contributes to a significant reduction in emissions.
The old heat exchanger probably leaked as a result of trips with substantial temperature changes during the past two years. Our end customer has tried to repair the heat exchanger, but this was not successful, partly because this type of heat exchanger is not very suitable for this purpose. In the meantime, the clock was ticking. A maintenance stop was scheduled for 10 weeks from now.
Tight deadlines and process optimisation
We are not just going to replace the heat exchanger here. This is also a good time to further optimise the processes. The end user would like to recover even more heat from the process, so we will have to calculate an additional heat exchange surface. The calculations are ready and the situation has been assessed. We know the optimal solution. The customer aims for delivery before the maintenance shutdown. Challenge accepted.
At Vahterus they work very hard to meet the tight deadline.
Plate & Shell heat exchanger as a solution
Because we clearly identified the problems and opportunities, we recommended a fully welded plate heat exchanger. Vahterus is the perfect partner in this case, because they build the so-called Plate & Shell heat exchanger, a round plate pack in a round casing. The round shape ensures that the heat exchanger is better at withstanding thermal stress. All the hard work paid off. We managed to deliver the heat exchanger 2 weeks before the desired delivery date. A big thank you goes to our Finnish partner Vahterus!
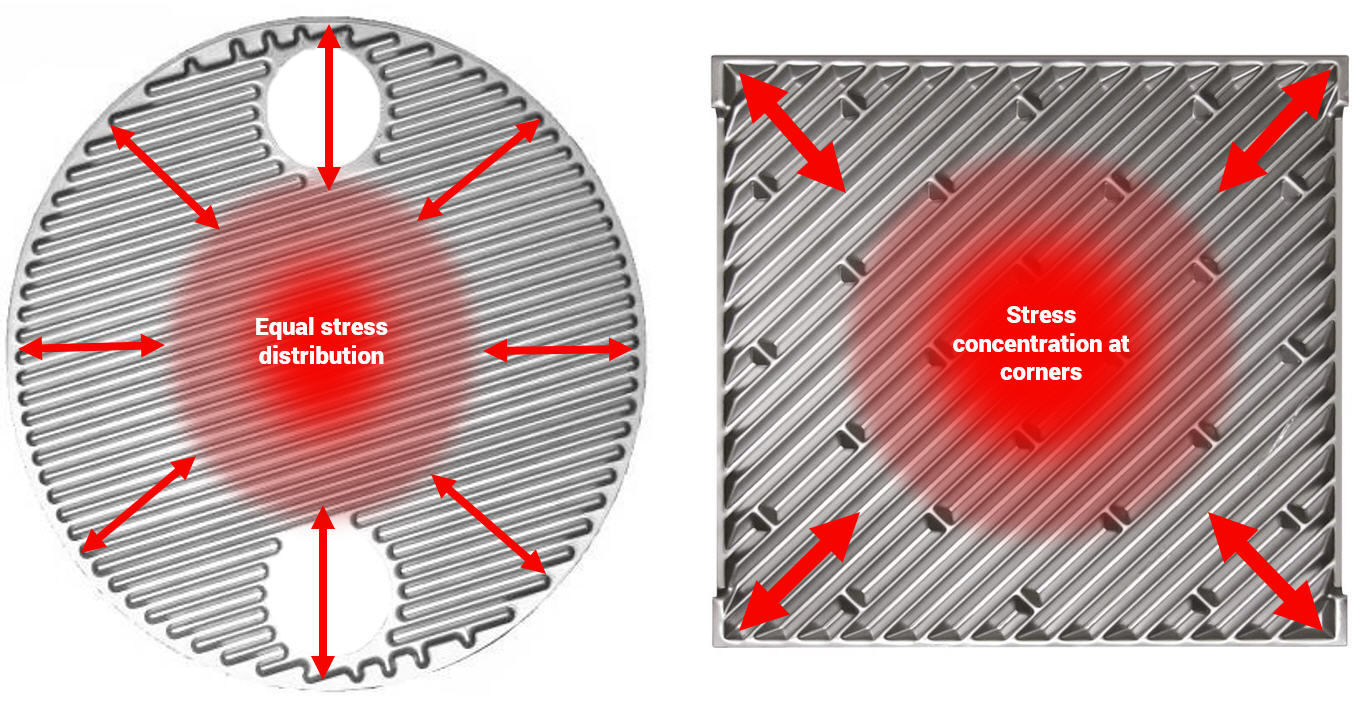
Efficient cooperation
Kapp’s capability to compare various types of heat exchanger always proves to be a great advantage. We are not tied to one type of heat exchanger or one manufacturer. We selected a Plate & Shell heat exchanger. Short lines of communication ensured that we were able to act within a very short time frame; within 24 hours the first calculations were available and on day 2 we visited the site to assess the situation. Despite the time pressure, Kapp facilitated an interim inspection at the manufacturer in Finland, which gave the end user even more confidence. We were able to deliver the heat exchanger to their site within 8 working weeks, after which the client was able to install the exchanger directly during the maintenance break. A successful project with many highlights, which could not have succeeded without the extremely efficient cooperation between the end user, Vahterus and Kapp.