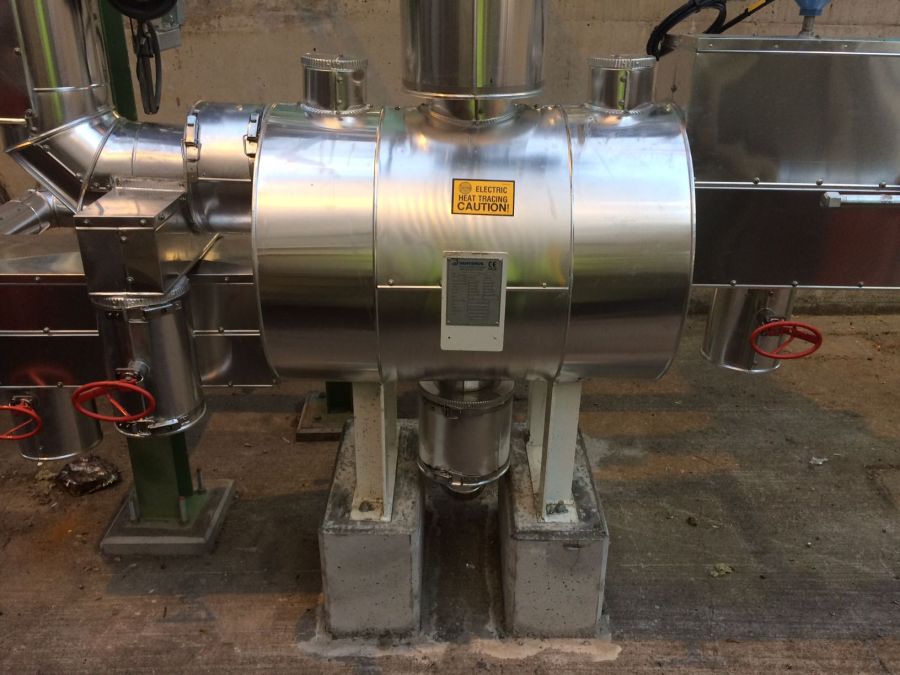
Vahterus plate & shell heat exchanger for chemical production site Antwerp
For a chemical production site in Antwerp, Kapp received an order for two Vahterus plate & shell heat exchangers. The application itself is not very complicated, but for the end customer this was THE solution to their problem. They were not familiar with the so-called plate & shell heat exchangers, this compact solution was a bull’s-eye for them.
The customer uses the first heat exchanger, type 4HH-200/2/1, as a heater. The product must be heated to prevent solidification during transport. The product is transported in insulated containers to a customer in Germany. Sometimes such a trip takes just a little longer than planned in advance. Before loading, the product is heated to 130°C to prevent it from solidifying. The heat exchanger comes into view here. Loading does not take place continuously, trucks are coming and going. To prevent the heat exchanger from blocking in between loading of various trucks, the product is circulated from a tank by the heat exchanger. The use of the heat exchanger is therefore cyclical. Due to product features, a welded heat exchanger was required. The Vahterus Plate & Shell, a welded plate heat exchanger without gaskets, was a perfect fit.
The customer uses the other heat exchanger (5HH-400/4/4) to pre-heat a feed stream to a reactor. Steam condensate on the primary side heats the product in the secondary trajectory. This exchanger replaces a block-type heat exchanger. Such an exchanger is less suitable for cyclic use and in this case the block exchanger was also leaking – unacceptable in a chemical environment.
The engineers of the chemical group did not know the Vahterus Plate & Shell heat exchangers yet. The fact that Vahterus has been producing these heat exchangers for more than 25 years gave them extra trust.