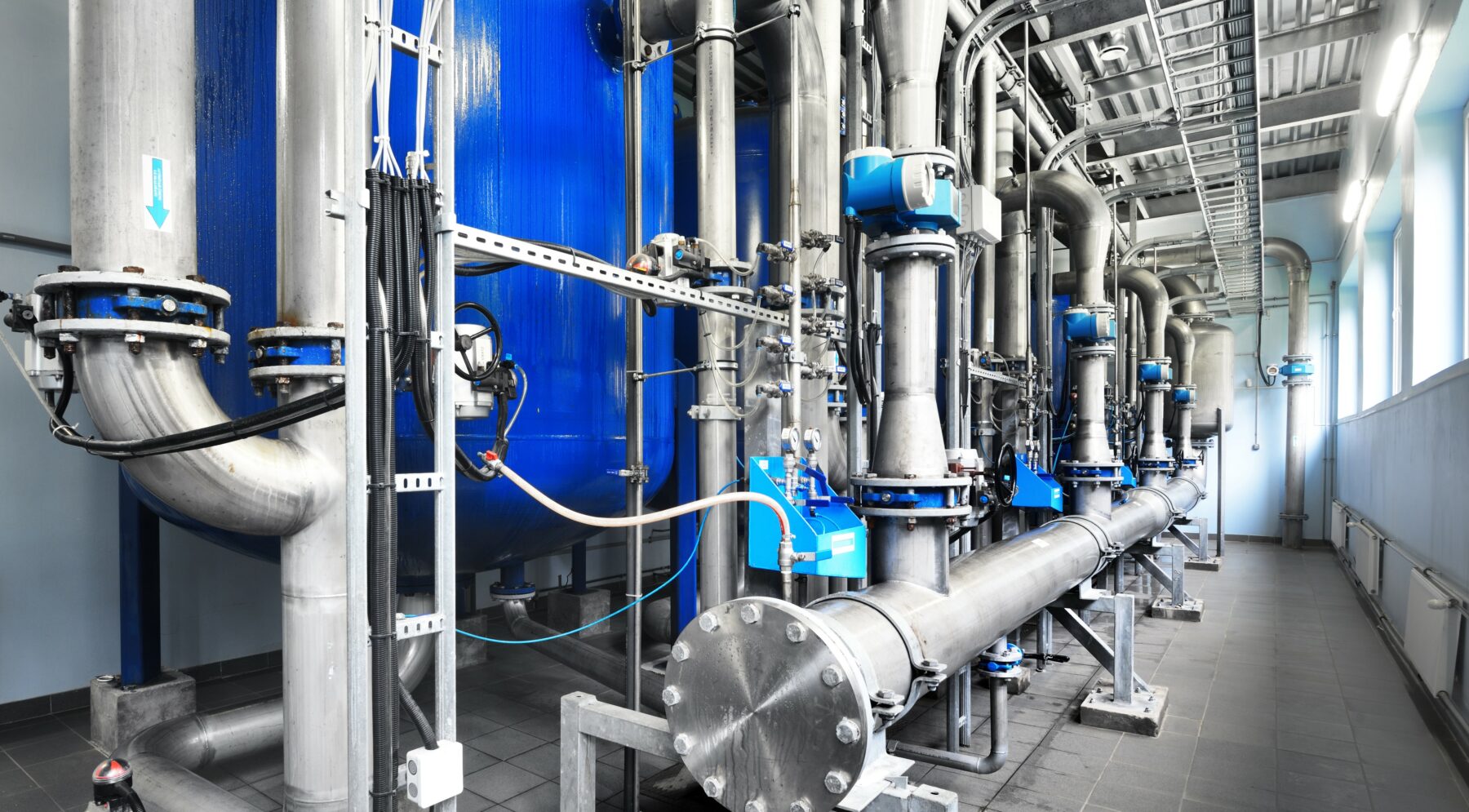
The future of electric process heating
The Thermon Quantum Truflow Heater™ marks the latest advancement in Thermon’s series of circulation heaters. Kapp is excited about this new technology, proudly considering it a significant leap forward. This heater delivers superior heat transfer performance compared to conventional electrical heaters, thanks to the Truflow Guide Technology. This technology mitigates the risk of overheating by promoting a consistent flow around heating elements, facilitating effective cooling – a concept we refer to as “No Tube in Window”. We are pleased to provide you this detailed explanation.
Challenge
Reinventing a well proven concept
It has always been a challenge to design an electric heater that delivers a specific power output while efficiently cooling the elements and transferring this power to the process. Consequently, heaters have been designed with a conservative approach to mitigate the risks of hotspots in low-flow areas. Traditionally, electrical process heaters were designed with a longitudinal flow configuration, placing the cold end at the inlet nozzle. This design featured a relatively large pitch and small rod diameter without baffles, resulting in low velocities within the shell and consequently low heat transfer. While the use of baffles somewhat improved the allowable heat flux, it also introduced the risk of hotspots due to eddies, dead spots, and other uneven distributions and variations in velocity. These hotspots not only posed a potential process risk but also led to a significantly shortened element lifespan. For these reasons, Thermon felt challenged to create a better concept.
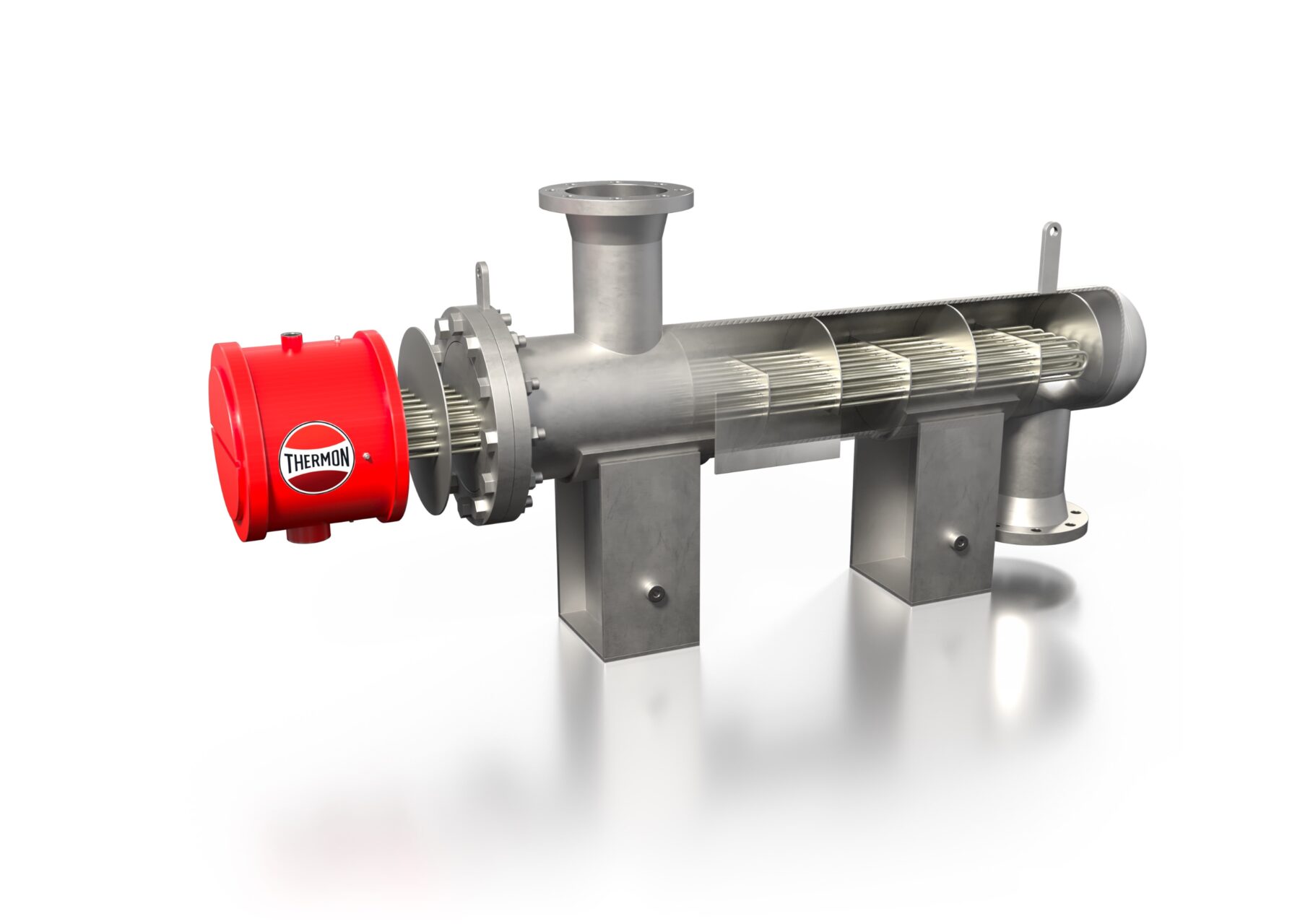
AMBITION
Smaller and better
A clear goal emerged from analyzing these challenges. Upon recognizing the potential, our main objective became to develop a compact electrical heater that would eliminate the challenges associated with traditional circulation heater technology. The aim was to deliver a significantly smaller and more powerful device. The established techniques of shell and tube heat exchangers have contributed to understanding the flow in a tube with baffles. Since dead spots occur mainly near windows, the idea was to omit the heating element in these areas. While this doesn’t eliminate the dead spots, it ensures that they do not cause problems. There were still a few steps to be taken before this idea could become a reality. It’s one thing to have an idea: the question of whether such an idea could work still had to be resolved using the modern engineering tools at our disposal.
SOLUTION
No tubes in window
Once started, progress was swift and the outcome was remarkable. The Thermon Quantum Truflow Heater is designed according to the “No Tube In Window” concept (NTIW concept). It has resulted in significantly more consistent sheath temperatures and a more compact heater design, eliminating hotspots. This not only translates to improved performance but also an extended element lifespan and reduced process risks. In essence, the NTIW concept involves omitting tubes in the part of the baffles where there is no overlap, known as the “window”. In the pursuit of an efficient heating appliance, this refined directional flow baffle design has proved indispensable. It improves heat transfer by reducing phase separation, creating controlled turbulence, and preventing stagnant zones. This results in higher heat transfer rates, compact heater design, and even heat distribution. The impact of directional flow baffles is generally well known: They mitigate dead zones and fouling risks, enhancing heat transfer efficiency while reducing cleaning and maintenance. The NTIW concept leads to energy savings and cost reduction due to lower temperature differences (ΔT) between the heating element and the process fluid. Moreover, our NTIW design allows for higher element watt density without overheating, enabling smaller and cost-effective heaters.
Engineering
Measuring, modelling and testing
When exploring a new concept, we need to adhere to the fundamentals: precise measurements, models, and real-life testing. It’s a methodical, step-by-step approach:
- Designing with HTRI
- Validating through ANSYS CFD
- Conducting lab tests with fiber optics to measure local sheath temperatures
- Incorporating all these findings, along with design factors and regulations, back into HTRI.
- Implementing Thermon Quantum Truflow Heater in real-life scenarios to observe its performance.
Successful tests gave the green light, The Thermon Quantum Truflow Heater™ is now in production.
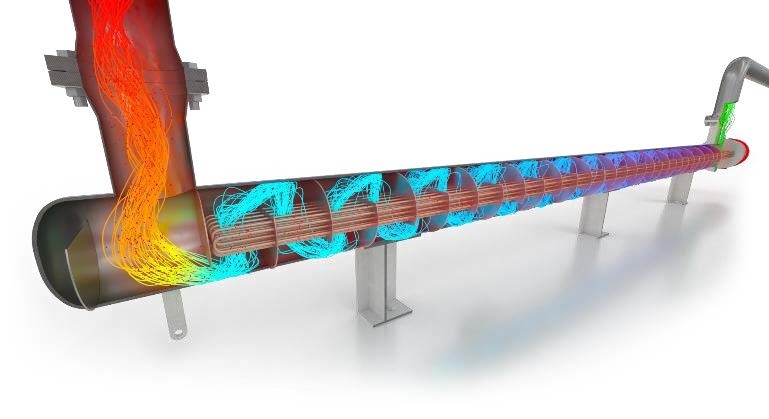
CONTACT
Interested in learning more about our innovative electrical heater design?
We understand that you may have unanswered questions. Please feel free to contact us, and we’ll be happy to discuss them with you.
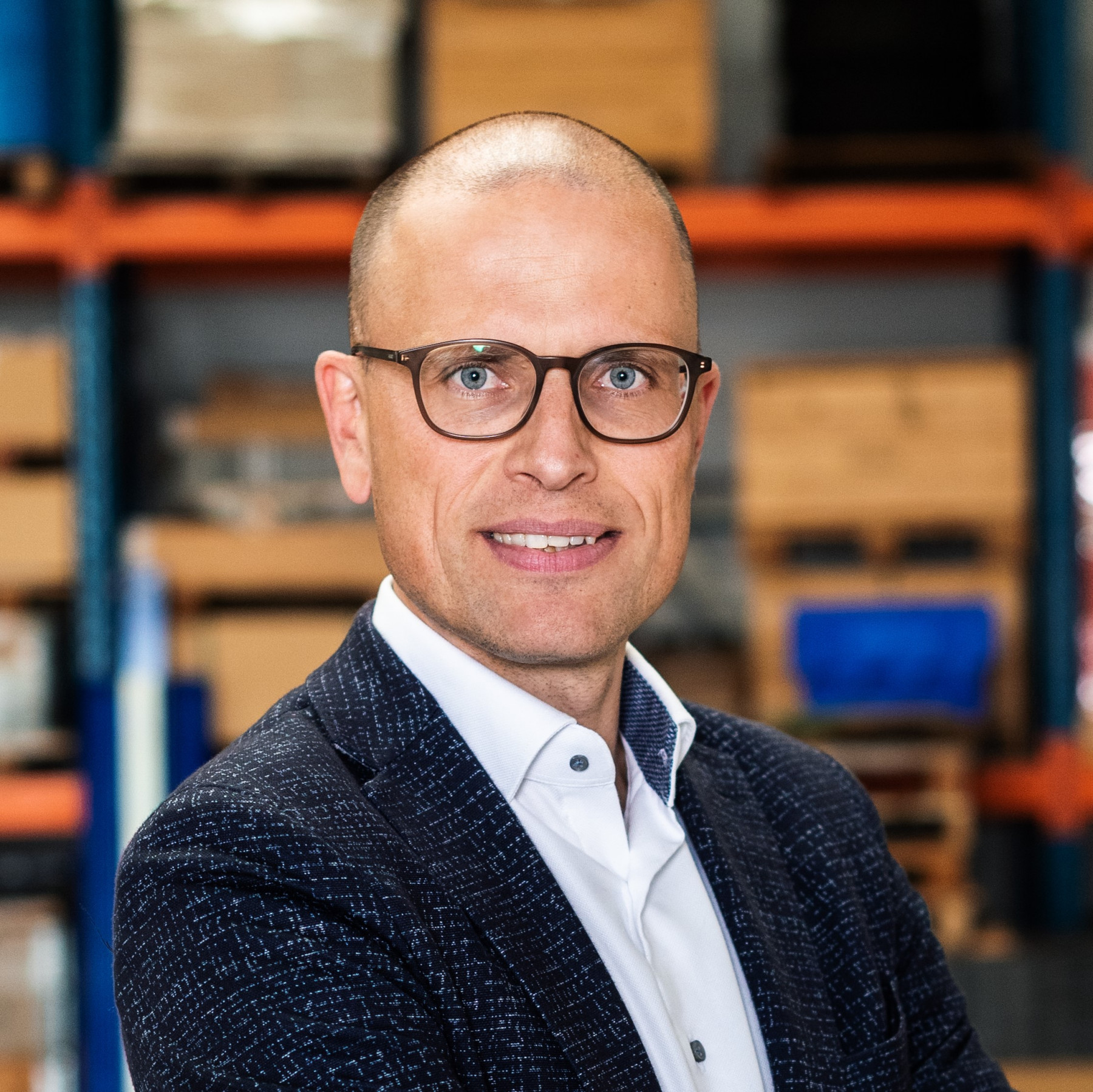