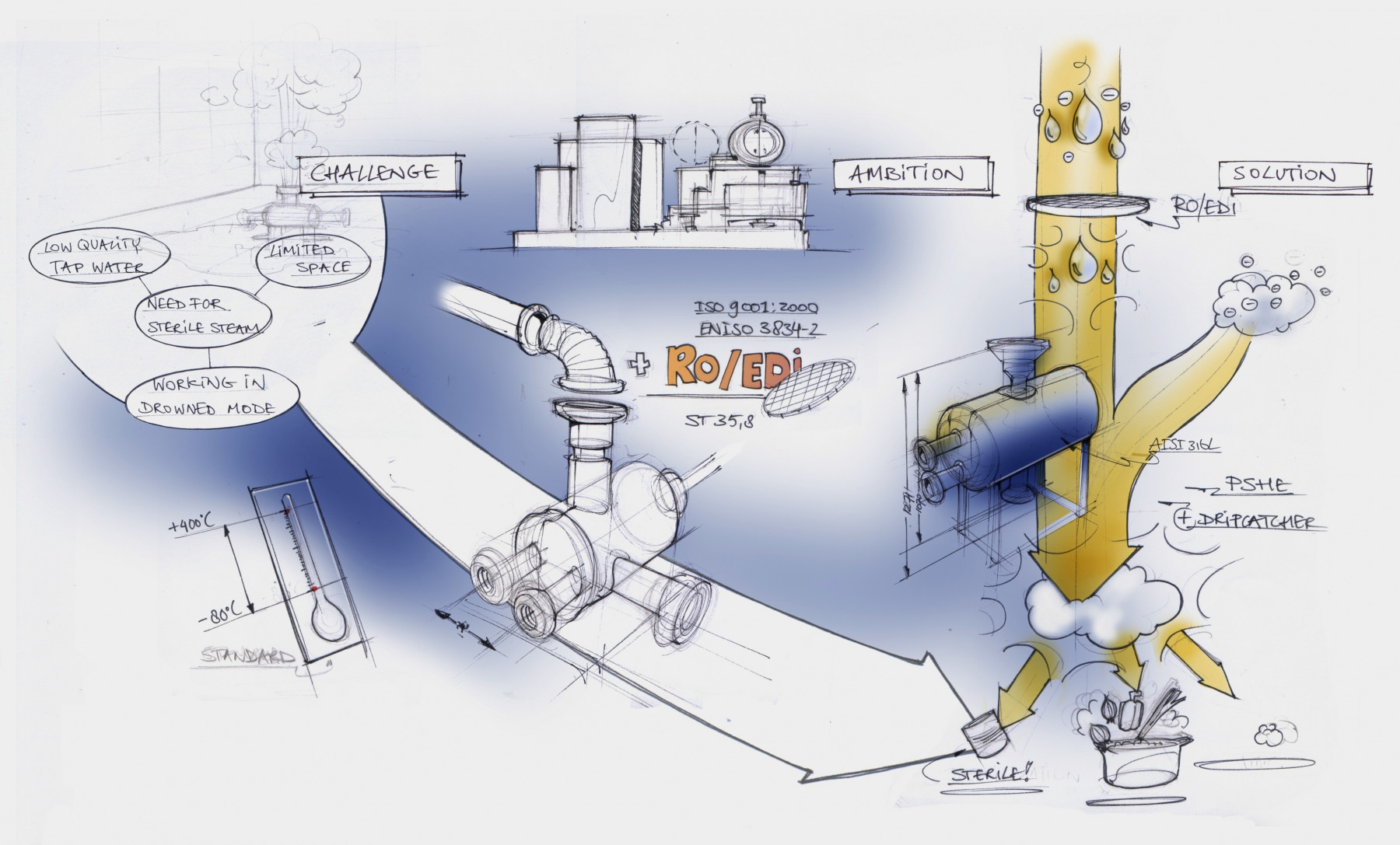
Soup!
First, people invented fire. Then they invented soup. Soup is one of the most ancient foods in the world. It is easy to make, tasty and quite healthy too. In most cases, a bouillon made of meat and bones serves as the basis. The marrow inside the bones contains lots of collagen. When the bouillon is ready, vegetables or meat are added. Some of the ingredients will fall apart during cooking; others will just become tender. Sometimes a little cream can be nice as well. Kapp went to Poland to turn on the heat in a soup factory.
The process
The soup in the factory is basically done in the same way as in your own kitchen, except of course for the size of the kettles and the way of heating. In Poland they use steam in order to bring the soup to a simmer. All the ingredients such as vegetables and beans are washed and then prepared in large kettles. From the kettles the soup passes through pipes to the packing department. Some of it is packed aseptically; some is packed in glass jars and tins. After sterilization the soup is cooled down in order to avoid loss of taste. After that, each unit is given a wrapper with information and then is ready to sell.
The project
Kapp’s job was to take care of the steam production inside the factory. The steam is produced in steam generators. A closed network of pipes brings the steam to the various places in the factory where it is needed. The quality of the tap water in Poland doesn’t meet the standards of the customer, so we needed to arrange for sterile steam, by using normal steam and softened, sterile water. It is done like this: before the softened water is evaporated in the steam generator, it passes through a so-called RO-EDI unit. This unit takes out all salts and minerals. In order to turn the water into steam, we use steam from normal tap water. The clean steam can be used for the preparation of foods and is suited for sterilization and direct steam injection.
The choice
The customer demanded a compact installation, combined with a drip catcher. The installation should also work in ‘drowned’ mode, which leaves a layer of condensate in the heat exchanger. In situations like these, a shell & tube exchanger is common. But they tend to be big, which wasn’t what we wanted for the construction of a compact skid.
Eventually, we opted for a plate & shell exchanger, which has a more efficient heat transfer capacity and therefore needs less space. A drip catcher was easy to combine because it is barrel-shaped. The total installation has very little loss of pressure, due to smart engineering and can be produced to individual client specifications – with various connections. The capacity of the installation is 4.000 kg of steam per hour, with an overpressure of 4 bar.
Kapp was awarded the assignment because of our flexible attitude, short production time and the right balance between price and technique. The installation has been supplied by Vahterus in Finland. The installation doesn’t need specific maintenance. The units will be cleaned by means of hot water or a CIP liquid. Because the complete unit has been welded, the cost of maintenance will remain low. Lime deposits inside the system are something to bear in mind, though.